24.05.23
Everything you need to know about Magnetic Drills
Overview
A magnetic drill, also known as a mag drill or magnetic drilling machine, is a specialized power tool used for drilling holes in ferrous (magnetic) materials such as steel and iron. Unlike traditional handheld drills, magnetic drills are designed with a strong magnetic base that attaches firmly to the workpiece, providing stability and precision during drilling operations.
Magnetic Drill Components
Here are the main components and features of a typical magnetic drill:
- Magnetic Base: The magnetic base is a key feature of a magnetic drill. It consists of a powerful magnet that adheres to the ferrous surface of the workpiece. The magnetic base ensures stability and prevents the drill from moving or shifting during drilling.
- Drill Head: The drill head houses the motor and controls of the magnetic drill. It is usually adjustable, allowing the drill to be positioned at different angles for drilling in various orientations (horizontal, vertical, or overhead).
- Drill Column or Arm: The drill column or arm connects the magnetic base to the drill head, providing the necessary support and rigidity. It allows for height adjustment and can often be rotated or pivoted to accommodate different drilling angles.
- Motor and Gearbox: Magnetic drills are equipped with a motor that provides the power for drilling operations. The motor is typically electric-powered and can have variable speed settings or fixed speed options. The motor is connected to a gearbox, which helps control the speed and torque output.
- Chuck or Spindle: The chuck or spindle is the mechanism used to hold and secure the drill bit or annular cutter. It allows for easy installation and removal of cutting tools, enabling quick tool changes during drilling operations.
- Controls and Safety Features: Magnetic drills have controls to operate the drill motor, including an on/off switch, speed control, and sometimes a reverse function. They may also feature safety mechanisms such as overload protection, magnetic holding force indicators, and safety interlocks to ensure safe operation.
- Coolant System: Many magnetic drills are equipped with a built-in coolant system or coolant attachment. This system provides a continuous flow of cutting fluid or coolant to the drill bit or annular cutter during drilling. The coolant helps lubricate the cutting tool, reduce heat, and improve cutting performance.
What are the applications of magnetic drills?
Magnetic drills are commonly used in construction, metalworking, fabrication, and industrial applications where precise and efficient drilling of ferrous materials is required. They offer stability, accuracy, and the ability to drill holes at various angles and orientations, making them a valuable tool in many drilling operations.
Advantages of using Magnetic drills
Using a magnetic drill press, also known as a mag drill or magnetic drilling machine, offers several benefits in various applications. Here are some advantages of using a magnetic drill press:
- Versatility: Magnetic drill presses are highly versatile tools that can be used for drilling holes in a variety of materials such as steel, iron, and other ferrous metals. They can handle a range of hole sizes and depths, making them suitable for different drilling tasks.
- Portability: Magnetic drill presses are designed to be portable and lightweight. They typically feature a magnetic base that adheres firmly to the workpiece, allowing the drill press to be used in various locations, including vertical, horizontal, and overhead drilling positions. This portability makes them convenient for construction sites, industrial settings, and other remote locations.
- Stability and Accuracy: The strong magnetic base of the drill press provides stability during drilling, ensuring precise and accurate hole placement. This feature is particularly beneficial for applications that require precise hole alignment, such as fabrication, metalworking, and construction projects.
- Increased Productivity: Magnetic drill presses are designed for efficient and rapid drilling. The combination of their magnetic base, powerful motor, and cutting tools enables faster drilling speeds and reduces labor time. This can lead to increased productivity and cost savings in projects where multiple holes need to be drilled.
- Safety: Magnetic drill presses offer enhanced safety features. The magnetic base provides a secure attachment to the workpiece, reducing the risk of slipping or movement during drilling. Additionally, many magnetic drill presses have built-in safety mechanisms, such as electronic overload protection and integrated coolant systems, which help prevent overheating and improve operator safety.
- Accessibility: Magnetic drill presses can be used in tight or confined spaces where traditional drill presses may not fit or be practical. Their compact size and ability to attach to vertical or overhead surfaces make them useful for drilling holes in areas that are difficult to reach with other types of drilling equipment.
It's worth noting that while magnetic drill presses have numerous advantages, they may not be suitable for all drilling applications. Factors such as material thickness, surface conditions, and specific project requirements should be considered when determining the appropriate drilling method or equipment to use.
Disadvantages of using Magnetic Drills
While magnetic drills offer several advantages, there are a few disadvantages to consider as well. Here are some potential drawbacks of using a magnetic drill:
- Limited to Ferrous Materials: Magnetic drills can only be used on ferrous materials such as steel and iron, as the magnetic base requires a ferrous surface to adhere to. They are not suitable for non-ferrous metals like aluminum, copper, or brass, or other non-metallic materials.
- Size and Weight: Magnetic drills can be relatively bulky and heavy compared to standard handheld drills. This can make them less portable and more challenging to maneuver in certain situations, especially in confined spaces or when working at heights.
- Initial Investment: Magnetic drills can be more expensive compared to traditional drills due to their specialized design and features. The cost of the magnetic drill and the accompanying annular cutters or accessories can be a significant investment for some users.
- Limited Drilling Depth: The drilling depth of magnetic drills is determined by the length of the annular cutters. While various cutter lengths are available, they may not provide the same drilling depth as certain traditional drill bits. For extremely deep holes, additional tooling or alternative drilling methods may be required.
- Cooling and Chip Evacuation: Magnetic drills typically include a built-in coolant system to lubricate and cool the cutting tools. However, in some cases, chip evacuation can be challenging, especially when drilling deep holes or with certain materials. Proper chip evacuation and cooling are crucial to ensure efficient and accurate drilling.
- Noise and Vibration: Magnetic drills can generate significant noise and vibration during operation, which can be discomforting for the operator. It is important to use appropriate personal protective equipment, such as hearing protection, to mitigate these effects.
Lubrication options
Cutting spray and cutting oil are both used as lubricants in machining processes to reduce friction and heat during cutting operations. However, there are some differences between the two:
Cutting Spray
- Form: Cutting spray is typically a liquid lubricant that is formulated as a spray. It is designed to be applied as a fine mist or aerosol using a spray bottle or nozzle.
- Application: Cutting spray is easy to apply and provides a thin, even coating on the cutting tool and workpiece. It is commonly used in light-duty machining operations, such as drilling, tapping, and milling.
- Cooling: Cutting sprays often contain a high percentage of water or water-based additives, which aid in cooling the cutting zone by dissipating heat generated during the cutting process.
- Chip Evacuation: The use of cutting spray can help in flushing away chips and debris from the cutting area, preventing chip buildup and improving machining efficiency.
- Convenience: Cutting sprays are convenient to use and can be easily stored and transported due to their liquid form and aerosol packaging.
Cutting Oil
- Form: Cutting oil is a liquid lubricant specifically formulated for machining operations. It is typically available in liquid form in bottles or drums.
- Application: Cutting oil is applied directly to the cutting tool or workpiece either by hand or through a lubrication system. It provides a continuous film of lubrication during the cutting process.
- Lubrication and Cooling: Cutting oil offers superior lubrication properties, reducing friction and wear on cutting tools and workpieces. It also provides better heat dissipation, helping to cool the cutting zone and prolong tool life.
- Heavy-Duty Machining: Cutting oil is commonly used in heavy-duty machining operations, such as turning, threading, and heavy milling, where higher cutting forces and temperatures are involved.
- Extended Tool Life: Due to its excellent lubricating properties, cutting oil can extend the life of cutting tools by reducing tool wear and improving cutting performance.
- Varieties: Cutting oils are available in different formulations, including straight oils (pure mineral oil) and soluble or emulsifiable oils (mixed with water). The choice depends on the specific machining requirements and the material being machined.
In summary, cutting sprays are often used for light-duty operations, provide cooling, and offer convenience in application. Cutting oils, on the other hand, excel in heavy-duty machining, offer superior lubrication and cooling properties, and are available in different formulations for various machining needs.
How to use a magnetic drill
Using a magnetic drill, also known as a mag drill or magnetic drilling machine, typically involves the following steps:
- Set up the machine: Place the magnetic drill on a flat and clean surface near the workpiece. Ensure that the surface is ferrous (magnetic) to allow the magnetic base of the drill to attach securely.
- Adjust the magnet: Most magnetic drills have an adjustable magnet with a lever or switch. Activate the magnet by flipping the switch or pulling the lever to engage the magnetic base. Make sure the magnet is securely attached to the workpiece to provide stability during drilling.
- Select the drill bit: Choose the appropriate drill bit based on the material being drilled and the desired hole size. Ensure that the drill bit is compatible with the magnetic drill's chuck or spindle.
- Install the drill bit: Open the chuck or spindle of the magnetic drill and insert the drill bit. Use the provided chuck key or spindle wrench to tighten the chuck securely, ensuring the drill bit is properly secured.
- Adjust the drilling speed: Set the desired drilling speed on the magnetic drill. Some models have a variable speed control, while others may have multiple fixed speed settings. Refer to the manufacturer's instructions for specific speed recommendations based on the material and drill bit diameter.
- Position the drill: Position the magnetic drill so that the drill bit is aligned with the desired drilling location on the workpiece. Ensure that the drill bit is perpendicular to the work surface for accurate drilling.
- Start drilling: Firmly hold the magnetic drill with both hands and apply moderate pressure on the drill. Switch on the drill motor and gradually lower the drill bit onto the workpiece. Use a steady and controlled motion to drill the hole, allowing the cutting edges of the drill bit to do the work.
- Coolant (if applicable): Depending on the drilling application and material, it may be necessary to use a cutting fluid or coolant to lubricate and cool the drill bit and workpiece. Follow the manufacturer's recommendations for the appropriate coolant and application method.
- Complete the drilling: Once the desired depth is reached, gradually lift the drill bit out of the hole. Switch off the drill motor and wait for the drill bit and machine to come to a complete stop before removing the magnetic drill from the workpiece.
Always refer to the specific instructions provided by the manufacturer of the magnetic drill for proper operation, safety guidelines, and any additional steps or considerations specific to the model you are using.
Types of Magnetic Drill
The two types of magnentic drill are normal sized ones and compact ones. The main difference between a normal magnetic drill and a compact magnetic drill lies in their size, weight, and intended applications. Here are some key distinctions:
- Size and Weight: A normal magnetic drill is typically larger and heavier compared to a compact magnetic drill. Normal mag drills are designed for heavy-duty drilling tasks and can have larger cutting capacities and drilling depths. Compact mag drills, on the other hand, are more lightweight and portable, making them suitable for applications where space is limited or where maneuverability is essential.
- Cutting Capacity: Normal magnetic drills generally have larger cutting capacities, allowing them to drill larger diameter holes and handle thicker materials. They are suitable for industrial or construction applications that involve drilling into heavy steel structures or large workpieces. Compact mag drills have relatively smaller cutting capacities and are suitable for lighter-duty drilling operations or situations where access is restricted.
- Power and Performance: Normal magnetic drills typically have higher power ratings and offer higher drilling speeds and torque output. They are designed for demanding drilling tasks that require more cutting force and power. Compact mag drills, while smaller in size, still offer sufficient power for their intended applications and can effectively handle a range of drilling requirements.
- Portability and Accessibility: Compact magnetic drills are designed to be highly portable and maneuverable. They are suitable for applications where mobility is crucial, such as working at heights or in tight spaces. Their smaller size allows for easier transportation and access to confined areas that may be challenging for normal magnetic drills.
- Versatility: Normal magnetic drills often come with a wider range of features and accessories, providing versatility for various drilling tasks. They may have adjustable heads, multiple speed settings, and additional functionalities such as tapping or countersinking. Compact mag drills are more streamlined in design and may have limited features, focusing primarily on essential drilling capabilities.
The choice between a normal magnetic drill and a compact magnetic drill depends on the specific drilling requirements, available workspace, portability needs, and the materials being drilled. If heavy-duty drilling and larger cutting capacities are necessary, a normal mag drill may be more suitable. On the other hand, if portability, maneuverability, and access to confined spaces are priorities, a compact mag drill would be a better choice.
Brands of magnetic drill
There are several reputable brands that manufacture magnetic drills. Here are some well-known magnetic drill brands:
- Hougen Manufacturing: Hougen is a prominent manufacturer of magnetic drills and offers a wide range of models suitable for various drilling applications.
- FEIN: FEIN is a renowned power tool manufacturer that produces high-quality magnetic drills known for their durability and performance.
- Evolution Power Tools: Evolution Power Tools specializes in innovative cutting tools, including magnetic drills. They offer a range of models suitable for different drilling needs.
- Metabo HPT (formerly Hitachi Power Tools): Metabo HPT produces a variety of power tools, including magnetic drills, known for their reliability and robust construction.
- Nitto Kohki: Nitto Kohki is a Japanese manufacturer that produces magnetic drills renowned for their precision, quality, and advanced features.
- BDS Maschinen GmbH: BDS Maschinen is a German company known for its precision magnetic drills. They offer a range of models with advanced features for professional drilling applications.
- Rotabroach: Rotabroach is a well-established brand known for its magnetic drills and cutters, providing reliable and efficient drilling solutions.
- Champion Cutting Tool Corp: Champion Cutting Tool Corp is a manufacturer of high-quality cutting tools, including magnetic drills, known for their performance and durability.
- Jancy Engineering Company: Jancy Engineering is a leading manufacturer of magnetic drills, offering a range of models suitable for various drilling tasks.
- Euroboor: Euroboor is a European brand specializing in magnetic drills and cutting tools, providing reliable and efficient solutions for drilling applications.
Magnetic Drill Bits
Magnetic drills typically use specialized drill bits designed specifically for magnetic drilling operations. These drill bits are often referred to as annular cutters or magnetic drill bits. Here are the main types of drill bits used with magnetic drills:
- Annular Cutters: Annular cutters are the most common type of drill bits used with magnetic drills. They are hollow cylindrical cutters with multiple cutting edges. These cutters remove material from the workpiece in the form of a cylindrical slug rather than traditional drill bits that create chips. Annular cutters are available in various diameters and lengths to accommodate different hole sizes and depths.
- Twist Drill Bits: While annular cutters are the primary choice for magnetic drilling, some magnetic drills may also support the use of twist drill bits. Twist drill bits are commonly used for pilot hole drilling or smaller diameter holes. They have a spiral fluted design that allows for efficient chip evacuation during the drilling process.
- Step Drill Bits: Step drill bits, also known as cone drill bits or unibits, are used for drilling multiple hole sizes with a single bit. These bits have a stepped design with gradually increasing diameters. They are often used for hole enlargement or deburring operations in metal and other materials.
It's important to ensure that the drill bits used with magnetic drills are specifically designed for magnetic drilling applications. These drill bits are typically constructed with high-speed steel (HSS) or cobalt steel to withstand the high torque and cutting forces generated during magnetic drilling. It's recommended to refer to the manufacturer's guidelines and specifications to select the appropriate drill bits for your magnetic drill model and specific drilling requirements.
Do you need to use pilot drill bits with Magnetic drills?
In most cases, a pilot hole is not required when using a magnetic drill with annular cutters. Annular cutters are designed to start drilling directly into the workpiece without the need for a pilot hole. The design of the annular cutter, with its multiple cutting edges and center pilot pin, allows it to self-center and initiate the drilling process.
The center pilot pin of the annular cutter serves as a guide and helps maintain the alignment of the cutter during drilling. It also assists in creating a clean and accurate hole without the need for a separate pilot hole.
However, there might be situations where a pilot hole is recommended or necessary. For instance, when drilling on curved or uneven surfaces, it can be helpful to create a pilot hole to ensure proper alignment and stability before using the annular cutter.
Additionally, for certain materials or applications, such as hard metals or thick plates, starting with a small pilot hole might make it easier to initiate the drilling process with the annular cutter.
It is essential to follow the recommendations and guidelines provided by the manufacturer of the magnetic drill and the annular cutters to determine whether a pilot hole is required for a specific drilling operation.
Should you buy or hire magnetic drills?
Whether it's worth buying or hiring a magnetic drill depends on several factors, including the frequency of use, the duration of the project, the available budget, and the convenience of ownership versus renting. Here are some considerations to help you make a decision:
Buying a Magnetic Drill:
- Long-term Use: If you anticipate frequent and ongoing use of a magnetic drill, purchasing one can be a cost-effective option. Owning a magnetic drill gives you the flexibility to use it whenever needed without additional rental costs.
- Convenience: Having your own magnetic drill allows you to have immediate access to the tool whenever required. You don't need to coordinate with rental companies or worry about availability.
- Familiarity and Customization: By owning a magnetic drill, you become familiar with its features, operation, and maintenance. You can customize it to your specific needs and preferences, such as selecting compatible accessories or optimizing cutting performance.
- Project Flexibility: With a magnetic drill at your disposal, you have the freedom to work on projects at your own pace and schedule, without the time constraints imposed by rental periods.
Hiring a Magnetic Drill:
- Infrequent Use: If you have occasional or one-time drilling needs, hiring a magnetic drill might be a more cost-effective solution. Hiring allows you to pay for the tool only when you need it, without the upfront investment of purchasing.
- Budget Constraints: If the cost of purchasing a magnetic drill exceeds your budget, hiring can be a more affordable option, especially for short-term projects.
- Access to Specialized Models: Hiring gives you access to a wide range of magnetic drills, including high-end or specialized models, which may be more expensive to purchase outright.
- Maintenance and Storage: Hiring eliminates the need for maintenance, repairs, and storage of the tool. You can simply return it after use without any long-term commitments or responsibilities.
Ultimately, the decision to buy or hire a magnetic drill depends on your specific circumstances. If you foresee frequent use and have the budget, purchasing a magnetic drill provides convenience, long-term cost savings, and customization options. However, if your drilling needs are infrequent or budget-driven, renting a magnetic drill can be a more practical choice, offering flexibility and access to a range of tools without the long-term commitment.
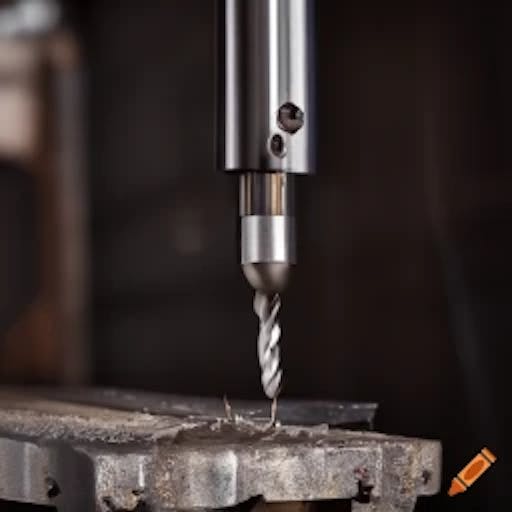