01.08.23
Choosing the right tools: Floor Grinder vs Floor Scarifier
When it comes to construction projects that involve concrete surface preparation, levelling, and coating removal, the selection of appropriate tools is crucial.
Selecting the right tool is the key to achieving superior results efficiently and cost-effectively on site.
Two commonly used machines for these tasks are the floor grinder and the floor scarifier. Although they may share similarities in their appearance, they serve distinct purposes and each offer their own unique functionalities.
Contents
To give you a good understanding of which tool best suits your specific project requirements, we will be exploring the following:
- Applications
- Features
- Advantages
- Limitations
- City Hire's surface preparation product range
Introduction to Floor Grinders and Floor Scarifiers
Floor Grinders
- Floor grinders, also known as concrete grinders or surface grinders, are highly versatile and heavy-duty machines. designed for surface preparation of concrete floors.
- They feature rotating discs or wheels with diamond segments that grind and polish concrete surfaces.
- Floor grinders are commonly used for concrete levelling, smoothing uneven surfaces, removing coatings, and achieving a polished finish for decorative applications.
- The diamond segments on the grinding discs or wheels are the primary tools responsible for removing material from the concrete surface. These segments come in different grit sizes, enabling operators to achieve various levels of surface roughness, from coarse grinding to fine polishing.
Floor Scarifiers
- Floor scarifiers, also called concrete scarifiers or milling machines, are powerful tools that utilise its rotating drums with hardened steel cutters or carbide-tipped flails to remove tough coatings, paints, and concrete from surfaces.
- Unlike floor grinders, floor scarifiers are typically used for more aggressive material removal. Floor scarifiers excel at removing thick coatings, rubber, and other stubborn substances from concrete surfaces.
- Floor scarifiers tend to be the number one choice for heavy-duty material removal tasks and concrete scarification on construction sites.
Floor Grinder Applications
Floor grinders are most commonly used for the following applications.
Concrete Levelling and Smoothing:
- Floor grinders are commonly used for concrete levelling and smoothing uneven surfaces.
- They can remove high spots, imperfections, and surface irregularities, creating a smooth and even foundation for subsequent flooring installations.
Coating and Adhesive Removal:
- Floor grinders are effective in removing old coatings, adhesives, and paint from concrete surfaces before applying new coatings or finishes.
- The diamond segments on the grinding discs can efficiently grind through various coatings and adhesives, preparing the surface for new treatments.
Surface Preparation:
- Before installing new flooring materials, such as tiles or epoxy coatings, floor grinders can meticulously prepare the concrete surface.
- By removing contaminants, old coatings, and surface irregularities, they create a clean and porous surface that enhances adhesion and prolongs the longevity of the applied coatings.
Concrete Polishing:
- Floor grinders equipped with fine-grit diamond segments can achieve a polished finish on concrete surfaces.
- This process enhances the aesthetics of the concrete, making it suitable for decorative flooring applications in commercial, residential, and public spaces.
Floor Scarifier Applications
- Coating and Paint Removal:
- Floor scarifiers excel at removing thick coatings, epoxy, mastics, and paints from concrete surfaces.
- Their robust cutting action efficiently breaks down and eliminates even the most stubborn materials, making them indispensable in projects where heavy machinery and chemicals have left lasting marks.
Concrete Scarification:
- Floor scarifiers play a crucial role in scarifying concrete surfaces, a process that involves aggressively removing layers of concrete to achieve specific depths or surface profiles.
- Scarification is particularly useful for levelling uneven surfaces, removing trip hazards, and preparing the surface for new overlays or coatings.
Rubber and Thermoplastic Removal:
- Floor scarifiers are highly effective in removing rubber deposits, thermoplastic markings, and other resilient materials from concrete surfaces.
- This feature makes them essential for road maintenance and airport runway projects where rubber build-up poses safety concerns.
Surface Cleaning and Texturing:
- Beyond material removal, floor scarifiers are also valuable for general surface cleaning and texturing applications.
- They can prepare surfaces for decorative overlays, achieve a slip-resistant finish, and create surface textures suitable for various applications.
Key components and features of Floor Grinders
Floor grinders possess several key features and components, contributing to their efficient performance:
Rotating Grinding Discs or Wheels:
- The core component of a floor grinder is the rotating disc or wheel, which has diamond segments attached to it.
- These segments are the grinding tools responsible for removing material from the concrete surface.
Depth Control:
- Many floor grinders offer depth control options, allowing operators to adjust the grinding depth according to the project's requirements.
- This feature ensures precise material removal and allows for variations in surface smoothing and coating removal depths.
Dust Collection:
- To minimise dust and debris during operation, floor grinders often come with built-in dust collection systems or the option to connect to external vacuum systems.
- Efficient dust collection will enhance the operators visibility and reduce any health hazards related to dust inhalation on site.
Manoeuvrability:
- Floor grinders are available in different sizes and configurations, including handheld, walk-behind, and ride-on models.
- This variety of options allow operators to choose which floor grinder is the most suitable for a specific project, providing manoeuvrability and ease of use, whether covering larger areas or working in confined spaces.
Key components and features of Floor Scarifiers
Floor scarifiers are equipped with various features that are designed for heavy-duty material removal.
Rotating Drums with Cutters or Flails:
- The heart of a floor scarifier is the rotating drum, which houses tough, hardened steel cutters or carbide-tipped flails.
- These cutters or flails are designed to withstand extreme force and abrasion, allowing them to break down and remove thick coatings, concrete, and other tough materials with ease.
Depth Adjustment:
- Similar to floor grinders, floor scarifiers often feature adjustable cutting depths. This capability enables operators to remove materials at the desired depth, accommodating various project requirements and optimising material removal efficiency.
Dust Management:
- Given the substantial amount of dust and debris generated during operation, floor scarifiers are equipped with dust collection systems or connections to external vacuums.
- Efficient dust management is essential for maintaining a clean and safe working environment and reducing exposure to harmful particles.
Self-Propulsion:
- Many floor scarifiers are self-propelled, enhancing their ease of control and manoeuvrability during operation.
- Self-propulsion allows operators to focus on the precision of the material removal task rather than expending effort on pushing the machine forward.
Advantages of Floor Grinders
There are plenty of advantages that can come with hiring a floor grinder.
Versatility:
- Floor grinders offer a wide range of applications, from levelling and smoothing uneven surfaces to removing coatings and achieving polished finishes.
- They are suitable for both small-scale and large-scale projects, making them highly adaptable tools for various construction and renovation tasks.
Concrete Polishing:
- Floor grinders equipped with fine-grit diamond segments can achieve polished finishes on concrete surfaces, enhancing the aesthetics of the concrete and providing a durable and attractive flooring solution.
Dust Collection:
- Floor grinders often come with effective dust collection systems or connections to external vacuums.
- This feature minimises dust during operation, creating a cleaner and safer working environment.
Indoor and Outdoor Use:
- Floor grinders can be used both indoors and outdoors, making them suitable for a variety of projects and environments.
Advantages of Floor Scarifiers
The advantages of hiring a floor scarifier are as follows.
Heavy-Duty Material Removal:
- Floor scarifiers excel at removing thick coatings, epoxy, and rubber from concrete surfaces, making them essential for industrial projects and surface repair work.
High Productivity:
- Due to their aggressive cutting capabilities, floor scarifiers can cover larger areas and complete material removal tasks faster than floor grinders.
- The increased productivity can expedite projects and reduce labour costs.
Trip Hazard Removal:
- Floor scarifiers are effective in eliminating trip hazards caused by uneven surfaces or damaged concrete, enhancing safety in various environments.
Roughened Texture:
- The scarification process creates a roughened surface texture, which is beneficial for improving the bond between the concrete and new overlays or coatings.
- This enhanced adhesion contributes to the longevity and performance of the applied coatings.
Limitations of Floor Grinders
Every tool has its limitations and a floor grinder is no different. These limitations are as follows.
Limited Aggressive Material Removal:
- While floor grinders are effective in removing coatings, they may not be as efficient or effective as floor scarifiers for thick coatings and paint removal.
- This limitation may lead to increased project duration and labour costs in coating-heavy projects.
Surface Damage Potential:
- If not used with care, floor grinders can potentially cause surface damage, especially on delicate surfaces or thin concrete.
- Operators must exercise caution to avoid unwanted surface disruptions.
Less Suitable for Scarification:
- Floor grinders are not specifically designed for aggressive scarification tasks, and their grinding action may not be as effective as a floor scarifier in such cases.
Limitations of Floor Scarifiers
A floor scarifier also have some limitations which should be considered.
Noise and Dust:
- Floor scarifiers produce more noise and dust compared to floor grinders. These factors may be a concern in sensitive environments or crowded work areas.
- Implementing proper dust collection and noise reduction measures is essential for mitigating these issues.
Less Precision in Smoothing:
- Achieving a precise and even surface finish with floor scarifiers can be more challenging, especially on irregular surfaces or when dealing with multiple layers of coatings.
- Operators will need skill and precision to obtain the desired surface outcome on site.
Factors to Consider When Choosing Between Floor Grinders and Floor Scarifiers
When deciding between a floor grinder and a floor scarifier for your construction project, it's essential to consider these key factors:
Project Scope and Scale
- Consider the scale of your project and the amount of material removal required.
- If you have a large industrial project that involves thick coatings or significant scarification, a floor scarifier may be the more suitable choice.
- For smaller projects or precision surface preparation, a floor grinder might be the better option.
Surface Condition
- Assess the condition of the concrete surface you'll be working on. If the surface is relatively flat with minor imperfections, a floor grinder may be sufficient to achieve the desired results.
- However, if the surface is heavily coated or damaged, the aggressive material removal capabilities of a floor scarifier may be necessary.
Surface Finish Requirements
- Consider the desired surface finish for your project. If you need a polished finish or a smoother surface with minimal texture, a floor grinder might be more suitable.
- On the other hand, if a roughened texture or improved adhesion is crucial, the rough cutting action of a floor scarifier may be advantageous.
Dust and Noise Considerations
- Evaluate the working environment and any specific requirements related to dust and noise levels.
- Floor grinders generally produce less dust and noise compared to floor scarifiers, making them more appropriate for indoor or noise-sensitive projects.
- Floor scarifiers may require additional dust collection and noise reduction measures to maintain a safe and conducive working environment.
Budget and Time Constraints
- Factor in your budget and project timeline.
- Floor scarifiers, while more powerful, may also be more expensive to rent or purchase.
- Additionally, their aggressive material removal might shorten the overall project duration, potentially affecting labour costs.
Operator Experience and Training
- Consider the experience and training of your operators.
- Floor grinders are generally easier to operate and require less training compared to floor scarifiers, which demand more skill and careful operation to avoid surface damage.
- Adequate training and operator competence are essential to achieving desired results and minimising potential hazards.
Conclusion
In conclusion, both floor grinders and floor scarifiers are invaluable tools in the construction industry.
They each have unique capabilities to cater to a diverse range of applications. Understanding their applications, features, advantages, and limitations is fundamental to selecting the most appropriate tool for your specific project needs.
Floor grinders offer versatility and efficiency, excelling in concrete levelling, coating removal, and surface preparation tasks.
They are suitable for both small-scale and large-scale projects, making them highly adaptable tools for various construction and renovation tasks.
Floor scarifiers shine in heavy-duty material removal, aggressive coating removal, and concrete scarification tasks. They are indispensable in industrial projects, road maintenance, and situations where robust material removal is paramount. The enhanced productivity of floor scarifiers can expedite projects and reduce labour costs.
By carefully analysing the requirements of your project and weighing the factors mentioned above, you can make an informed decision and ensure that you have the right tool to achieve the best results in the most efficient and cost-effective manner.
Whether you choose a floor grinder or a floor scarifier, having the proper equipment will undoubtedly contribute to the success of your construction or renovation project. Adequate operator training and safety measures will ensure the tools are used optimally and safely, enhancing the overall project outcome.
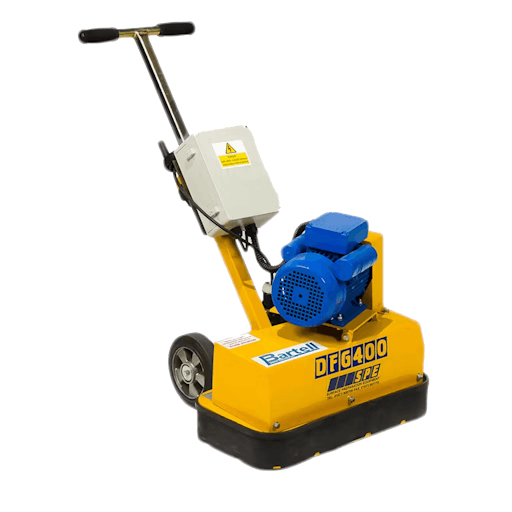